It seems as though, recently, fighting games are making a major resurgence on the gaming scene. Games like Street Fighter IV, BlazBlue, and Tatsunoko versus Capcom are bring the genre back to the forefront of gaming. The fighting genre was absolutely HUGE during the 1990's when Mortal Kombat and Street Fighter ruled the arcades and consoles alike; the games were meant to be enjoyed in the arcade. There is just no better way to play a fighting game than with a nice, quality arcade joystick and button combination in front of you. If you want to be a major competitor in any of these games, you are going to need the equipment necessary to play like one.
There are many options out there for anyone who wishes to take their fighting games to the next level. Mad Catz in particular is a company who has been making this controller option accessible to consumers though it often comes at a hefty price. This is in no way meant to disparage the products that are produced by companies like Mad Catz, it is just that the expense of those sticks can often create a barrier that prevents gamers from getting the tools that they desire. If you fall into this category where you would love to have a quality arcade stick for use on your home console but cannot or are not willing to invest as much money as they ask for them in stores, it is my hope that this guide can help you achieve that goal. Let me state, up front, that neither myself nor Gaming Nexus is not responsible for any damage done to any controllers or products that you buy in an attempt to build your own stick. Dismantling and altering these products will void your warranties and nullify any claims that you may have on the performance of said products. Proceed at your own risk.
If you are still here, let's get down to business. The truth of the matter is that you can build your own, high quality arcade controller for merely a fraction of the price as those offered in stores. As long as you know what you need and some basic soldering skills, then you can have your own competition level stick in no time. In this tutorial, we are going to create an arcade joystick for use on the Xbox 360. This stick will also function on the PC.
Part 1: Gathering your materials
The first thing that you need to do is to gather your materials. You will need, minimally, the following items:
Third Party controller- I recommend using a 3rd party for two reasons: cost and simplicity. The cost of unofficial controllers is generally a lot cheaper than the first party offerings. The simplicity of their PCB boards is often night and day from the official controllers as well, making your task a ton easier in the long run. The first party controllers are often laid out slightly differently in the manner that the generally share ground connections between the buttons, making soldering and wiring for their boards more complicated than the simplified boards of third party controllers. In my project, I used a Mad Catz 360 Arcade Gamestick. These particularly controllers have hit the clearance bins of many stores; I know that Fry’s for example sells them for $4.99 if you can find them in stock. Most of Mad Catz’s controllers use similar boards though, so you will do fine with any of their controllers. You can also check Gamestop as they had Gamestop branded controllers for about $20 used or $25 new. This is potentially the most expensive single part for the project, so shop around and find yourself a good deal.
Joystick- I used and recommend using the Happs Competition joystick, mainly because I prefer the physical feel of their products. The general consensus online is that the Japanese, Sanwa parts are superior, but this is the brand that I have come to know and love. This particular joystick can be purchased for $13.95 directly from
Happs. Another site,
Lizard Lick Amusements sells the exact same joystick for $7.95, which is a great deal but I have never dealt with them personally. There are other joysticks out there to use, some cheaper and others more expensive but this is a custom job, so get one that you like.
Pushbuttons- If you are going to wire the entire 360 controller, meaning all buttons and the d-pad (no need for the analog sticks), then you will have to wire 11 pushbuttons in total (A, B, X, Y, L, R, LB, RB, Start, Back, and Guide). For this stick in particular, I was very shortsighted and only wired 8 buttons, leaving out the L, R and the Back buttons. When I get around to finalizing the case, I will be adding these buttons but it will not take much additional work. I went with Happ’s competition grade parts for my pushbuttons, which sell for about $2.20 a piece; they do offer discount for bulk orders of 25 or more on the buttons, so that is an option if you are trying to cut costs and are considering building more than one joystick. There are various styles of pushbuttons available too, which I plan on utilizing in my final design Things like the traditional “Player 1” start buttons and such are purely cosmetic and don't effect the performance of the final product. As a word of advice, when you order your pushbuttons, make sure that they come with all required components to hook them up, namely the necessary cherry switches; both Happs and Lizard Lick include all of the necessary parts.
Soldering iron- Soldering irons can be purchased fairly cheaply at stores like Radio Shack. I don’t care much for the expensive, digital soldering irons, just give me the plain old simple iron. Radio Shack has a nice beginner’s soldering set for about $8, which includes the iron, solder, holder, and a few small tools to help. This particular kit will more than suit the needs for this project.
Wire- While you are at Radio Shack, grab a spool of small wire; if you don’t want to drop the coin to buy some, then just splice open a phone cord and use the individual wires from inside (yeah, I can be frugal). It will also serve your best interests to try and get solid wire rather than threaded wire; I used threaded and it turned out okay, but I got tired of dealing with stray connections in the long run. Make it easy on yourself and try to get solid wire.
Solder- Your iron will more than likely come with a stock of solder, if not, get some as they are only a couple of dollars.
Hot Glue Gun- In this project in particular, I found hot glue to be the ultimate compliment to solder. Coating your connections in hot glue after ensuring a clean, soldered connection can ensure your connections stay in place and do not interfere with one another.
Case- The actually building of a case for the joystick could be another tutorial in itself. For my purposes, and since I was just trying this for the first time and wanted to create more of a test box, I simply used a cardboard banker’s box. This is another thing that would purely be up to you and your tastes. In the end, before you start battling fierce competition, you will want to build a solid casing for your controller. The banker’s box that I used did not hold up well to prolonged usage
Various small tools- You will want to keep the typical reference tools around like screwdrivers; there will be need form some small things throughout the project.
Part 2: Let's crack open that controller
This is where the screwdriver will come in handy. You will need to remove the casing from the controller and remove the PCB board from the inside. Please, please, please take your time with this. You do not want to scratch or damage the PCB board as that could impair the functionality of the controller. This is not hard a hard process, but at can be tricky because depending on the controller that you use there may be different types of screws use and many of the buttons on the controller may inhibit the ability to remove portions of the casing. Take your time and everything will eventually come apart. Eventually, once everything is stripped away, you should have a bare PCB board with all of the required connections clearly visible. Once it is in your possession, set it aside and keep it safe until we get to the soldering portion.
Part 3: Mounting the joystick and pushbuttons
This could vary depending on how nice of a case that you decide to utilize. Using the cardboard banker’s box was quick and easy and ultimately the perfect option for my first attempt. Assuming that you go with a more secure and permanent casing, this could take longer to prepare. It is completely up to you to decide what you want to use.
Once you know what you are going to use, you will need to decide on the sort of button layout that you will want to use. There are tons of options in this department, depending on how many buttons you want to use and what your layout preference may be. The two main layouts that you will see available across the Internet are the standard American SF layout, which involves 6 (or 8) buttons laid out perfectly straight in horizontal fashion and the Japanese SF layout. The Japanese layout involves buttons that are placed in an arc fashion which matches the natural lay of your fingers. When I built my, I decided to go with the second layout which is the traditional Japanese SF setup. It really is just a matter of personal preference and I prefer the natural feel of the Japanese layout.
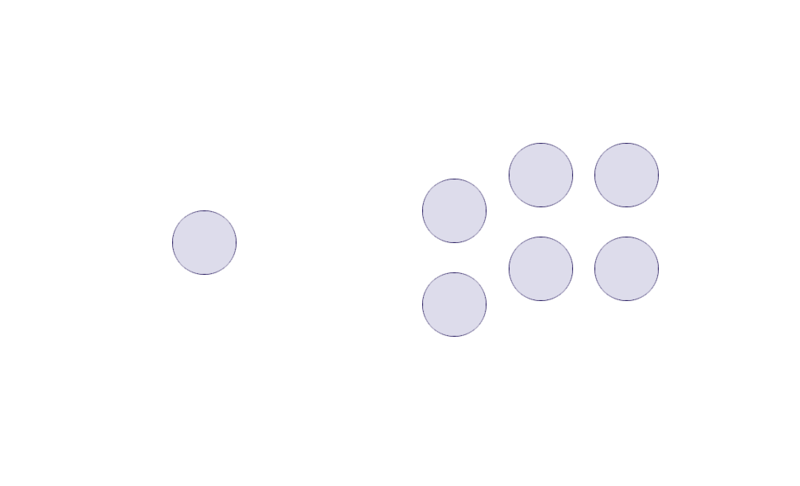
You can use various templates from online sites to get a standard spacing scheme for your buttons, but I prefer to lay them out myself and cater the design to the layout of my hands. When I laid out the buttons, I used a washable marker and colored the tips of my fingers. I then let my hand lay naturally on the surface where my buttons would be and let the natural position of my fingers dictate the spacing that I was going to use for the pushbuttons. In the end, the final result just felt better to me personally.
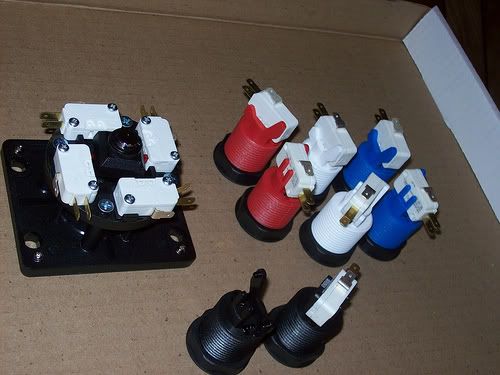
Once the layout is marked, simply cut the holes for each of your buttons and the joystick. The joystick will more than likely come with the paper template to utilize in cutting the space out on your actual case. It will likely require 4 or more screws to secure it in position. The pushbuttons on the other hand simply slide into position from the top and have a button that you will screw onto it from the bottom, securing them in place.
Part 4: Solder the connections on the PCB
This part requires some soldering experience, though it can be done with minimal experience as I had. If you are not comfortable using the soldering gun, do not be afraid to practice ahead of time in order to ensure a steady hand and quality connections. It is also very easy to completely ruin your PCB by melting something that you should not, so get comfortable before doing the actual work. The connections on the PCB are usually pretty obvious in their layout as they look exactly like the controller itself. There will be two wires per button which will be your ground and your actual connection. Take your time and make sure to make good, solid connections and avoid bridging two or more separate connections. Solder will conduct a signal, so you do not want it "leaking" towards other contact points.
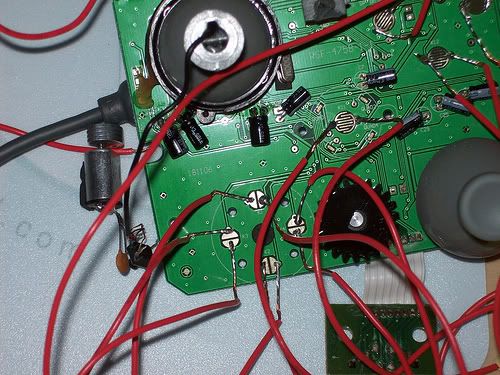
Decide if you want to do straight, solid connections between the PCB and the controller, or if you want to wire the control board and buttons separately and then connect them at a later time. I went with the second option since it gave me more room to work with in the long run. When I move to the final casing though, I intend on using one straight connection just for the sake of creating a higher quality connection. Just make sure that you give yourself some length if you are going to use one wire as it will help eliminate the stress of pulling on your soldering points.
For the purposes of this project, I found it best to simply heavily “tin” your wires ahead of time. What this means is that you will melt and place a heavy coating of solder on the connecting tip of your wire before you even go near the board. After this is done, it will be very easy to simply make your connection on the board and add a little heat, melting the existing solder on your wire and allowing it to connect to the board.
Once you have all of your wires tinned, you can proceed to actually soldering them to the actual PCB board. As I stated previously, each button will have to wires connected to it; it doesn’t matter which one will be used for the ground, do not worry about that, just ensure that you have clean, solid connections and that you use the same wire for the ground on the other end. After you have soldered the connections, you can test them by plugging the controller into your system or into your PC, and then touching the other end of the wires together for a particular button. If you have done it correctly, closing the bridge between the two wires should trigger the button and the system should recognize and register the button press.
You will do this for each of the following connections on your PCB board:
A, B, X, Y, Back, Guide, Start, L, R, LB, RB, d-pad UP, d-pad DOWN, d-pad LEFT, and d-pad RIGHT.
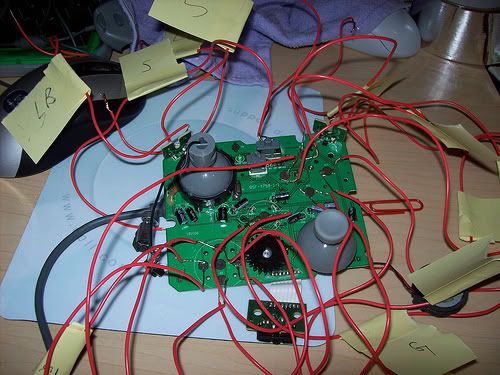
In the end, there will be a lot of wires. You may want to consider using small stickers, or perhaps using different colored wires to keep things organized in the long run. I did not do this originally and it turned into a nightmare in the end. Eventually I just grabbed some sticky notes and labeled them for the time being which worked out well. Once you have them all soldered and tested, it is time to put some hot glue over the connection points. Hot glue does not conduct a signal and it keeps your connections secure. Failing to do so will result in you pulling a connection free at some point in time, so it is better the handle it now than later.
Part 5: Wire your buttons
Now, this will be the same whether you are using a different set of wires which you will connect to the corresponding wires that run from the PCB board or you will be running the wires directly from the board to your buttons. Connecting the buttons is actually rather simple. The Happ’s brand controllers use a series of what are called “Cherry Switches”. These are simple, little relays that will be the functioning part of your buttons that actually make the connection to signal the actions. Each button has its own Cherry Switch and the joystick uses four, one for each direction.
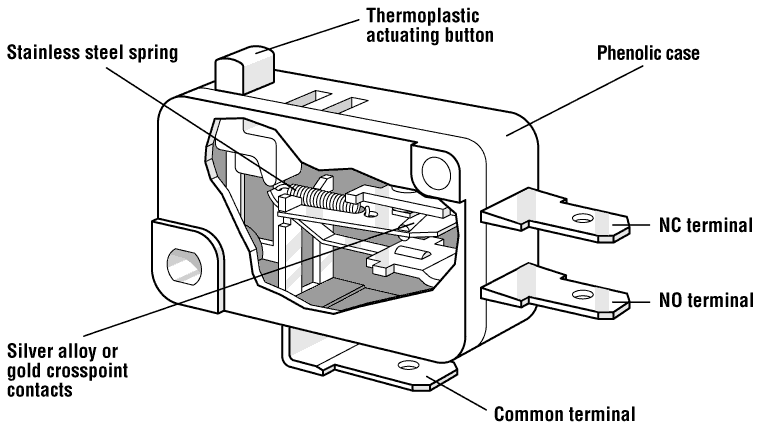
Each Cherry Switch has three connection points, one on the bottom which is the Common Terminal, also known as your ground, and two coming out of the side which are labeled as NC (normally closed) and NO (normally open). They should be labeled though it may be hard to see and / or read; the connection closest to the ground is the NO terminal. For our purposes, we will only be using the Common (ground) and NO terminals.
As I stated earlier, it does not matter which wire goes where, just as long as you are using the same two wires for a particular button. If not, you will drive yourself nuts troubleshooting the issue and retracing your wires. This is another reason that I went with the two wires which I would connect together in the end route; it made it easier to ensure that I was using the correct connections. Once the Cherry Switches are connected to the PCB board, you can test them before you seat them into the button casings. As long as the testing worked following the soldering, this should be a no-brainer process.
Now, it is very important to note which Cherry Switch is which when you wire the joystick. Take a second and look at how the joystick actually works. When you press the joystick in the down direction, it actually triggers the Cherry Switch that is in the up position, and the same for left and right; pressing left triggers the right one and vice versa. I found it beneficial to take a small Sharpie and label the joystick Cherry Switches accordingly. I pressed Left on the actually joystick and then wrote an L on the Cherry Switch that it triggered… and then did the same with each direction. Once I did that, it was as simple as connecting the wires from d-pad LEFT to the Cherry Switch labeled accordingly.
Part 6: Secure your case
Hopefully, assuming that everything went smoothly for you, that should really be all that you have to do. Once you have
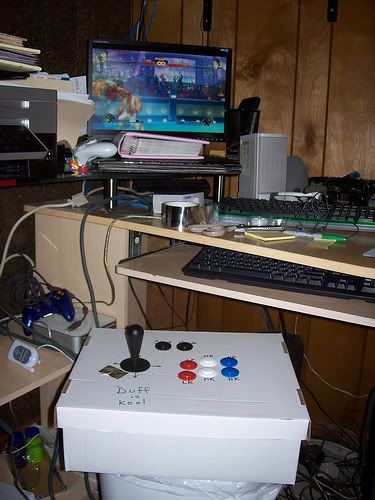
everything connects and shored up, simply secure everything in position in your case, plug it in, and have a ball.
Part 7: Enjoy
There you go, your own arcade joystick that now function on your home console. Please feel free to
contact me with questions. I will be more than happy to help and or point you in the direction of resources to help you create your own stick.